Why Every Workplace Needs an Emergency Action Plan (EAP)?
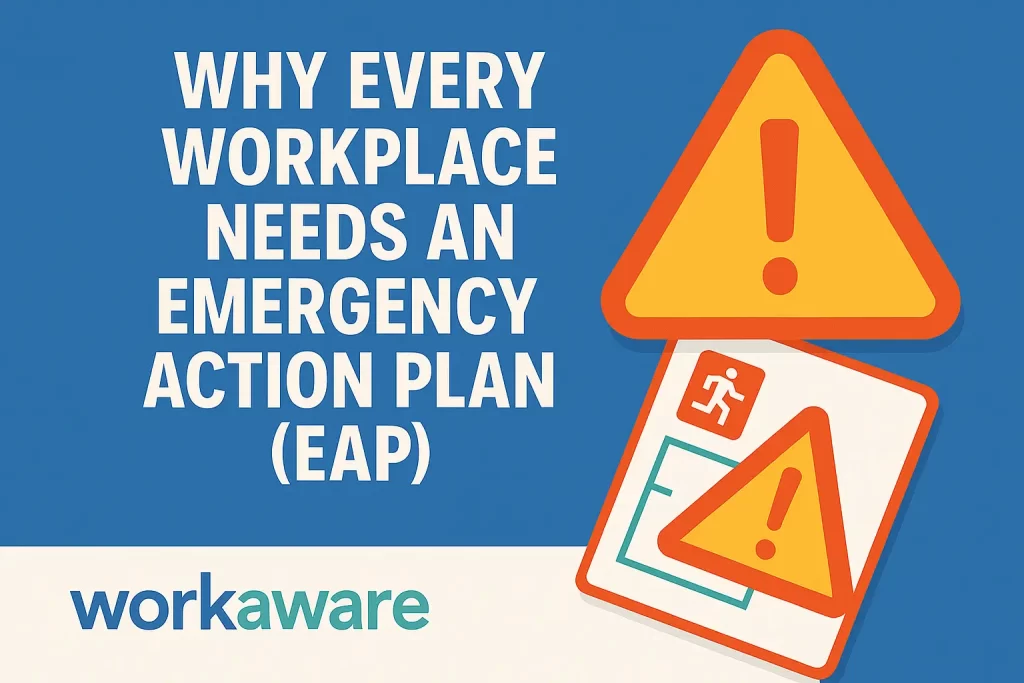
This guide explains what an Emergency Action Plan (EAP) is, why it’s legally required, and how to design one. Topics include risk assessment, role assignments, communication protocols, training practices, and regular review. Use this structured checklist to craft or update your EAP.
Emergencies in the workplace from fires and chemical spills to active threats and power outages don’t wait for a plan. Yet many organizations still lack a structured, updated Emergency Action Plan (EAP).
Whether you’re managing a manufacturing plant, a construction site, or a corporate office, a well-crafted EAP is required by OSHA and essential for protecting your people, operations, and legal compliance.
In this guide, we break down:
What an Emergency Action Plan is (and why it matters)
The top components every EAP should include
How to train your team effectively
How digital tools like WorkAware simplify planning, compliance, and communication
Let’s dive into what makes a strong Emergency Action Plan and how to build one that actually works in a crisis.
What Is an Emergency Action Plan (EAP)?
An Emergency Action Plan (EAP) is a written document that OSHA (Occupational Safety and Health Administration) requires for workplaces with more than 10 employees, under standard 29 CFR 1910.38. It outlines employees’ actions during workplace emergencies such as fires, chemical spills, natural disasters, or workplace violence incidents.
Key Components of an Emergency Action Plan
Top 7 Components of an Effective EAP
- Risk Assessment
Identify potential hazards (fires, chemical spills, natural disasters, etc.) specific to your workplace or industry. Clear Evacuation Procedures
Outline exit routes, assembly points, and special protocols for employees with disabilities.Assigned Roles & Responsibilities
Define emergency coordinators, floor wardens, first-aid responders, and communication leads.Emergency Communication Plan
Set up alert systems, contact protocols, and post-incident reporting procedures.Employee Training & Drills
Conduct regular training and unannounced drills to ensure readiness.Post-Incident Procedures
Include incident reporting, medical response, and workplace recovery protocols.Routine Review & Updates
Review your EAP at least annually or whenever there are workplace changes.
Why Is an Emergency Action Plan Important?
Beyond fulfilling a legal requirement, an EAP can significantly enhance your organization’s preparedness and resilience in the face of unexpected incidents. Here’s how:
1. Enhances Employee Safety
Emergencies happen unexpectedly. With an EAP, employees know exactly what steps to follow during critical situations like fires, earthquakes, active shooter events, or toxic exposure. This clarity reduces panic, streamlines evacuation, and minimizes injuries or fatalities.
Example: During a fire drill at a mid-sized manufacturing plant, employees with prior EAP training evacuated the facility 40% faster than teams without training, highlighting how preparation can save lives.
2. Ensures OSHA Compliance
Compliance with OSHA’s emergency planning requirements is mandatory. Failure to comply can lead to citations, fines, and increased liability. In addition to OSHA 1910.38, industry-specific standards may require additional preparedness measures, particularly in high-risk sectors like construction or chemical manufacturing.
Pro Tip: OSHA provides a model EAP template that can be adapted to your workplace conditions.
3. Reduces Emergency Response Time
An EAP creates structure and predictability in chaotic situations. By assigning specific roles and responsibilities, such as evacuation coordinators or first aid responders, your business ensures everyone knows what to do without hesitation. This reduces confusion and enables faster decision-making.
4. Minimizes Business Disruptions
Emergencies can grind operations to a halt. An effective EAP addresses the immediate crisis and includes a business continuity plan that outlines how to resume essential functions. Reducing downtime helps prevent financial losses, maintain productivity, and protect your reputation.
5. Builds a Strong Safety Culture
Employees are more engaged and committed when they feel safe. A robust EAP demonstrates that the organization is proactive about workplace safety. This investment in team member well-being boosts morale, retention, and trust in leadership.
Office Insight: In one corporate setting, implementing an EAP improved team member satisfaction scores by 15%, with staff reporting they felt more secure and valued by management.
Real-World Applications of Emergency Action Plans
Let’s look at a few real scenarios where an EAP made a difference:
- Healthcare Facility: Thanks to its EAP, a hospital in Texas successfully relocated patients from one wing to another during a storm warning, minimizing risk and ensuring continuous care.
- Educational Institution: A school district implemented lockdown drills as part of their EAP. During an actual security incident, students and teachers acted quickly, reducing potential harm.
- Small Business: After a localized power outage, a retail store followed its EAP to evacuate customers safely and restore operations using a generator and an alternate payment system.
How to Develop an Effective Emergency Action Plan
Creating an EAP doesn’t have to be overwhelming. Here’s a step-by-step guide to help you craft a plan tailored to your organization’s needs:
1. Conduct a Workplace Risk Assessment
Identify potential emergencies that could affect your workplace. This includes internal threats (e.g., electrical fires, chemical spills) and external ones (e.g., floods, earthquakes, civil unrest).
2. Involve Employees in the Planning Process
Employees who participate in safety planning are more likely to understand and follow emergency procedures. Gather feedback from various departments and include employees with specialized knowledge.
3. Define Evacuation Routes and Assembly Points
Use clear, visible signage and make evacuation routes accessible for individuals with disabilities. Conduct regular evacuation drills to reinforce the process.
4. Assign Roles and Responsibilities
Assign specific roles, such as fire wardens, floor supervisors, first aid providers, and communication leads. Provide role-specific training to ensure they can carry out their duties effectively.
5. Develop Communication Procedures
Ensure you have a way to communicate both internally and externally during emergencies. This may include loudspeakers, text alert systems, two-way radios, or emergency contact lists.
6. Train Employees and Conduct Regular Drills
Training shouldn’t be a one-time activity. Schedule annual or semi-annual refresher courses, and test different scenarios during drills to identify gaps in your plan.
7. Review and Update the EAP Regularly
Changes in workplace conditions, new machinery, staffing changes, or building renovations can impact your emergency plan. Review your EAP at least once a year or after any significant change or incident.
Legal Requirements for an EAP
Per OSHA regulations:
- Workplaces with more than 10 employees must maintain a written EAP.
- Employers must review the plan with each team member when it is developed, whenever a team member’s responsibilities change, and when it is updated.
Adhering to these requirements can result in OSHA citations, fines, or increased liability in the event of an incident.
The Takeaway
An Emergency Action Plan (EAP) is not just a bureaucratic checkbox; it is an essential tool that protects lives, preserves property, and ensures the continuity of operations during unexpected events. By investing in a robust, well-communicated, and frequently updated EAP, your organization fosters a safety culture, boosts team member confidence, and stays prepared for challenges.
Frequently Asked Questions About Emergency Action Plans (EAPs)
An Emergency Action Plan (EAP) improves workplace safety, reduces response time during emergencies, and ensures legal compliance with OSHA regulations. It helps protect employees, minimize property damage, and maintain business continuity. A well-prepared EAP also reduces panic, outlines clear evacuation procedures, and designates roles so everyone knows what to do in a crisis saving lives and limiting disruptions.
Yes. According to OSHA regulations, businesses with more than 10 employees are legally required to have a written Emergency Action Plan (EAP). This ensures the safety of employees during emergencies and helps organizations remain compliant with workplace safety laws.
An Emergency Action Plan should cover a wide range of potential workplace emergencies, including:
Fires
Natural disasters (like earthquakes, floods, hurricanes)
Chemical spills or hazardous material exposure
Power outages
Acts of workplace violence or other security threats
The EAP should be customized based on the specific risks associated with your business or industry.
Typically, the safety manager or human resources (HR) department takes the lead in developing the EAP. However, the most effective plans are created with input from multiple departments, including operations, facilities, and senior leadership. A collaborative approach ensures the EAP is thorough and practical for all teams involved.